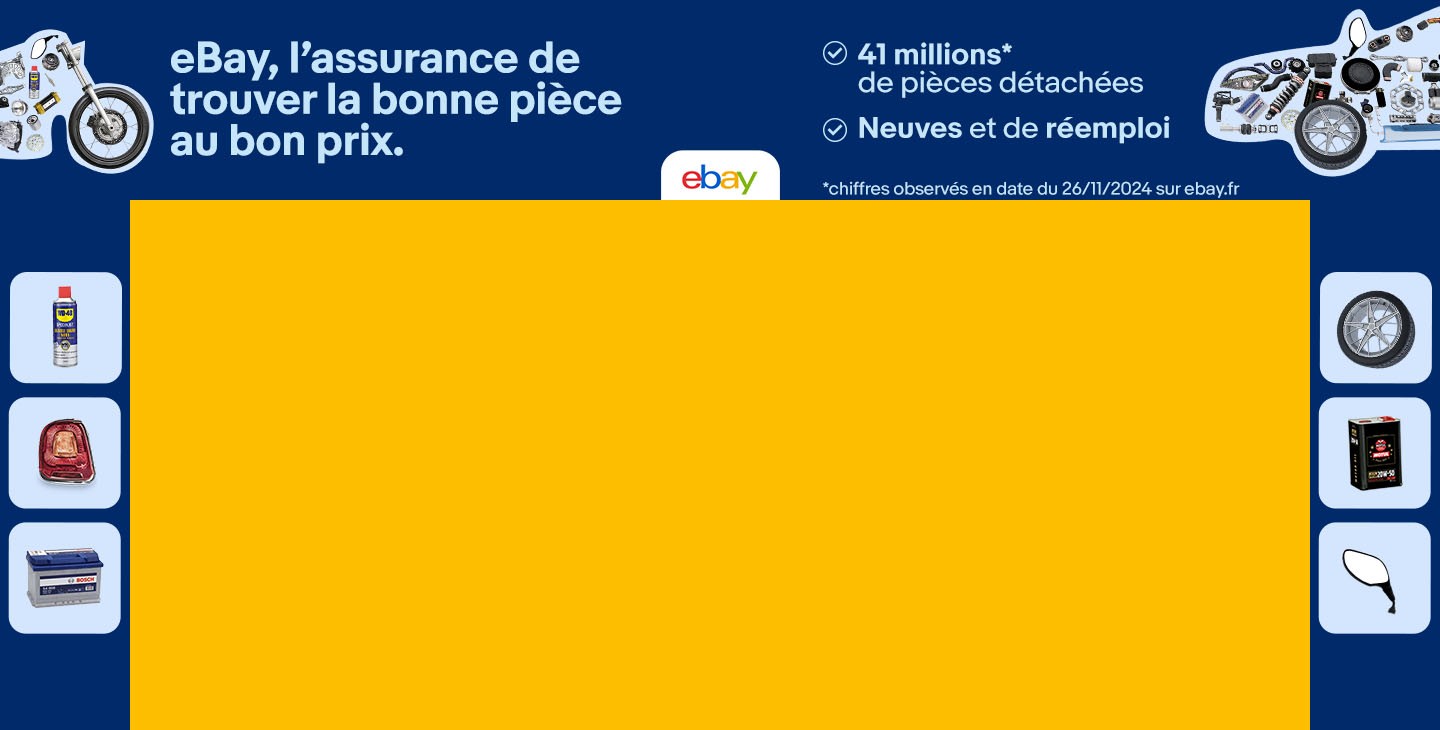
Atelier : relever le défi de la vraie productivité
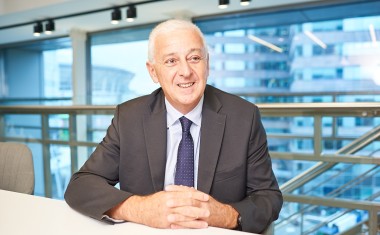
Une solution qui peut augmenter de 30% la productivité effective d’un atelier à périmètre constant ? C’est ce que préconise Didier Félice, fort d’une méthode déployée avec succès dans quelque 150 ateliers. Une méthode valable pour les grandes comme les petites structures...
Ne plus confondre productivité et efficacité de l’atelier, c’est le crédo développé par Didier Félice, «Special Adviser» pour l’Europe de « Road to Reliability » et son module dédié à l’entretien-réparation baptisé «Maintenance Planning & Scheduling». Le diagnostic de D. Félice, issu de son expérience de directeur de l’après-vente Europe de TIP, est clair : le temps réellement passé outil en main dans un atelier, quel que soit l’univers (dont l’entretien- réparation VP comme VI), dépasse trop rarement... 35 à 40% !
Infinité de détails
Un chiffre étonnant quand la plupart des ateliers revendiquent des scores de productivité qui dépassent souvent et largement les 80%. Une apparente contradiction que Didier Félice explique simplement : dans un atelier qui affiche d’aussi jolies performances, toutes les heures liées à une opération de maintenance entrent dans ce calcul de productivité. Et dans un atelier qui ne pense pas son organisation avec une approche industrielle, les heures non-efficaces –celles passées sans un outil en main– peuvent donc compter pour 60 à 65% dans ladite productivité !
Les motifs de non-efficacité d’un atelier se logent diaboliquement dans une infinité de détails quotidiens. Tous selon lui sont le fruit d’une approche trop empirique d’une activité qui ne remet pas à plat ni repense ses process. Un parking trop lointain ou trop difficile d’accès où l’on doit aller chercher et ramener le véhicule ; une mauvaise gestion de la file d’attente des véhicules entrant en atelier ; une réception mal faite qui oublie d’identifier des prestations dont il faut ensuite improviser l’exécution.... Et un cortège de motifs d’interruptions : une pièce difficile à trouver en magasin (jusqu’à une heure d’attente), inadaptée voire manquante (remontage nécessaire du véhicule mis en attente) ; un outillage absent ou son technicien dédié indisponible, des compétences mal employées, etc., etc.
En finir avec la culture du « pompier »
Autant de situations d’urgence, synonymes de déplacements et d’actions multiples, dont le chef d’atelier comme le productif font les frais : le premier passe dès lors son temps à éteindre des incendies qu’une bonne planification amont des prestations permettrait très souvent de ne pas allumer ; le second s’interrompt de multiples fois dans l’attente d’une solution dont il ne devrait pas avoir besoin (voir encadré). «Il suffit de poser un podomètre sur le chef d’atelier pour savoir si l’atelier est bien organisé : s’il fait 10 000 pas par jour dans un atelier de 10 productifs, c’est que tout le process est à revoir», calcule D. Félice. Il le proclame : «un atelier qui ne sait pas planifier son activité une semaine à l’avance n’est pas assez bien géré».
Il y a bien sûr les interventions imprévues. Mais là aussi «une bonne organisation doit permettre de les intégrer harmonieusement aux flux planifiés sans les désorganiser», assure-t-il.
Séréniser et fidéliser
Faut-il attendre des miracles d’une organisation repensée de l’atelier ? Oui, et surtout actuellement, quand l’après-vente devient une priorité absolue en multimarque comme en distribution VN, souligne Didier Félice. «Un atelier qui déploie parfaitement nos méthodes issues de notre plan “Maintenance Planning & Scheduling” (Préparation & Ordonnancement en bon français) peut espérer atteindre 55 à 60% de productivité effective», promet-il. Et 55 à 60% de temps passé outil en main contre 35 à 40%, «c’est l’équivalent de 3 recrutements évités pour un atelier de 10 productifs», rappelle-t-il.
Une solution donc à la pénurie de candidats comme à la rentabilité de l’activité après-vente. Mais une solution aussi, directe comme indirecte, au turn-over mortifère pour l’organisation d’un atelier :
- directe, car un atelier bien organisé accroît la fidélité du productif par la sérénité et la fluidité de sa mission quotidienne. Un atout concernant la nouvelle génération de techniciens qui veut un poste organisé, avec une mission bien définie, un outillage adapté et le tout, dans le cadre d’horaires précis, voire adaptés, qui permettent d’arbitrer sereinement vie professionnelle et vie personnelle.
- indirecte, car l’intégration d’un nouveau mécanicien «coûte en moyenne 6 mois de salaires dans le recrutement et la formation... et si le recruté reste !», conclut D. Félice.
Reste le rôle essentiel du chef d’entreprise. S’il ne priorise pas une telle refonte organisationnelle qui peut accroître à la fois l'efficacité, la rentabilité et la stabilité de son ou ses ateliers, la culture du pompier reprendra toujours le dessus...
Associer le chef d’atelier et les productifs
Doit-on considérer le chef d’atelier comme LE responsable d’une faible productivité ? Évidemment pas, souligne Didier Félice. «Un chef d’atelier est formé au management, à la technique, mais rarement aux processus d’un atelier ; culturellement, il évalue dès lors son efficacité à sa fonction de pompier quand il devrait être sensibilisé et surtout formé au contrôle à la fois organisationnel et financier de l’atelier».
Et c’est là que l’on reboucle sur la méthode « Maintenance Planning & Scheduling ». Elle préconise d’aider le chef d’atelier à se hisser au rôle de planificateur en lui faisant toucher du doigt les interactions entre activité atelier et compte de résultats. «Il doit être associé à la refonte des process et pouvoir concevoir et/ou utiliser des indicateurs mesurant par exemple le temps d’accès et de remplacement des pièces, le séquencement d’une opération et être souvent formé à la complexe organisation des flux entrant dans l’atelier», liste-t-il.
Une approche qui, pour être pleinement efficace, doit aussi impliquer les productifs qui doivent, en pleine conscience, revisiter leurs gestes techniques et identifier les ruptures de flux.
Sur le même sujet
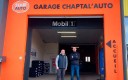
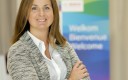
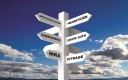
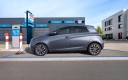
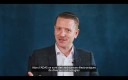
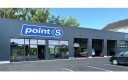
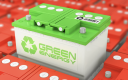