
Les règles de l’art concernent aussi le collage
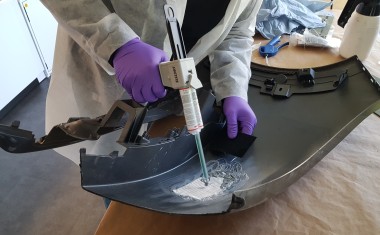
Présent en première monte comme en après-vente avec ses marques Loctite et Teroson, Henkel insiste sur le strict suivi de recommandations constructeur dans le rivetage-collage des éléments plastiques et métalliques des véhicules. Et compte sur son partenaire CESVI France pour diffuser ces principes dans ses formations.
Henkel, en après-vente, c’est bien évidemment Loctite. La marque, connue aussi du grand public, est principalement réservée aux applications mécaniques mais aussi aux réparations de petits éléments de fixation peu complexes. Côté carrosserie, cependant, les grands éléments de tôlerie et de vitrage, qui contribuent à la résistance de la structure-même du véhicule, se collent en Teroson.
Henkel ou l’expertise OEM
Fort de ces deux fers-de-lance du collage, le géant mondial de la chimie aux 22,4 Mds € de CA, dont 11,2 Mds sur les seules technologies d’adhésifs, d’étanchéité et de traitement de surface, peut se permettre de jouer les prescripteurs auprès des réparateurs. D’autant que deux phénomènes parallèles et complémentaires poussent les constructeurs à laisser de côté le soudage pour lui préférer le collage.
D’abord, l’électrification des véhicules et leur alourdissement par la batterie, qui pousse au gain de poids pour conserver l’efficience du groupe motopropulseur et les promesses de réduction d’émissions polluantes. Ensuite, le développement de matériaux composites et l’assemblage de métaux – acier et aluminium en particulier – qui nécessitent davantage de sécurité au moment de la réparation, le risque explosif étant important.
Le collage, allié de poids
Si bien qu’aujourd’hui, un véhicule moyen embarque 17 kg d’adhésif ! Et depuis qu’il est collé plutôt que jointé, et feuilleté plutôt que simplement trempé, le pare-brise peut améliorer de 40 % la rigidité de la carrosserie. A titre d’exemple, sur le marché nord-américain, 26 mètres d'adhésifs structuraux sont utilisés par véhicule. L'utilisation de seulement 1 kg d'adhésifs peut réduire le poids du véhicule de 25 kg. Et les inserts structurels peuvent réduire le poids du corps en blanc et de la fermeture de plus de 40 kg. Aussi Henkel s’est-il fixé pour objectifs de créer de nouveaux utilisateurs finaux et de nouvelles applications.
Une mission confiée, en France, à ses treize ingénieurs-commerciaux et deux techniciens formation qui effectuent plus de 710 sessions en atelier chaque année, auxquels s’ajoute, en complément, des modules d’e-learning. « Le digital démultiplie notre audience. Et si le client est formé à la bonne technique de réparation, il y a de fortes chances qu’il choisisse nos produits », plaide Christophe Valadié, directeur des ventes France & Benelux de Henkel. La technique, ou plutôt les techniques. Car Henkel revendique un savoir-faire de pointe sur les trois façons majeures de remettre en état un véhicule.
Reconstruire, remplacer, réparer
D’abord, reconstruire : « les tâches fréquentes impliquent la reproduction des joints d’origine des constructeurs ainsi que les réparations nécessitant l’assemblage de pièces métalliques et en plastique. La reconstruction représente souvent une alternative qui permet de gagner du temps et des ressources, par rapport au remplacement de pièces », explique-t-on chez Henkel. Répliquer les joints d’origine constructeur est un exemple de prestation sur lequel la marque Teroson a acquis une expertise inattaquable.
Ensuite, remplacer : « Les dommages structurels nécessitent la découpe des anciennes pièces avant le remplacement par de nouvelles. Compte tenu de la taille des pièces à remplacer, et de la nécessité de conserver l’intégrité structurelle du véhicule, une résistance structurelle élevée est indispensable ». Enfin, réparer : « les petites réparations sont les éléments qui peuvent être réparés relativement facilement, par exemple des attaches cassées du pare-chocs, ou des pièces d’une complexité similaire ». Ce qui convient particulièrement aux éléments plastiques.
CESVI France en partenaire-clef
Des méthodes dont Henkel met à l’épreuve le résultat par le biais de crash-tests spécifiques certifiés TÜV : le véhicule est emmené à 64 km/h et subit un impact frontal avec un angle de 40°, « plus conforme au réflexe d’évitement de l’automobiliste en approche d’un choc », relève Christophe Valadié. Les produits et méthodes Henkel, en France, font de Teroson la marque la plus labellisée en carrosserie par CESVI France, qui compte à son catalogue de formations plusieurs modules mettant à profit l’expertise du fabricant. Compte tenu des contraintes de la réparation automobile actuelle – mise en sécurité des VE/VH, réglage des ADAS, méthodes spécifiques à chaque conducteur – Henkel et CESVI France rappellent l’impérieuse exigence de travailler avec des produits répondant aux exigences des constructeurs. « Le contexte actuel, en particulier côté hausse des coûts, incite à faire des économies sur les produits... Mais un produit moins performant peut engendrer pertes de temps et non-respect de la qualité », insiste François Brodier, ingénieur carrossier & accidentologie au technocentre CESVI.
Sur le même sujet
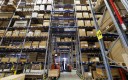
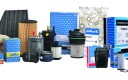
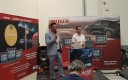
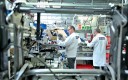
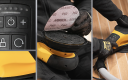
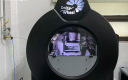