
Tuto Zepros Carrosserie - Masticage : petits trucs pour éviter les surprises désagréables

Les occasions de mastiquer un élément de carrosserie sont multiples. Méthodologie à employer et mastic approprié varient selon plusieurs critères. Ils dépendent des surfaces et défauts « à rattraper », de leur étendue, de la profondeur des dommages, de leur emplacement, de la nature des matériaux à mastiquer. Présentation.
1) Quel mastic utiliser ?
Les cas et les spécificités de la carrosserie automobile nécessitent l’utilisation de plusieurs types de mastics. Les fabricants proposent donc des gammes très étoffées.
Certes, il y a le mastic universel, le passe-partout, qui offre l’intérêt et le confort de ne pas avoir une kyrielle de boîtes de produits dans un placard. Néanmoins dans certains cas, mieux vaut avoir LE produit adapté comme par exemple :
• Le mastic multifonctions, un produit polyester multi-support et ultra léger, élaboré aussi bien pour les réparations d’imperfections que pour la finition sur acier nu ou galvanisé, ainsi que sur l’aluminium et ses alliages.

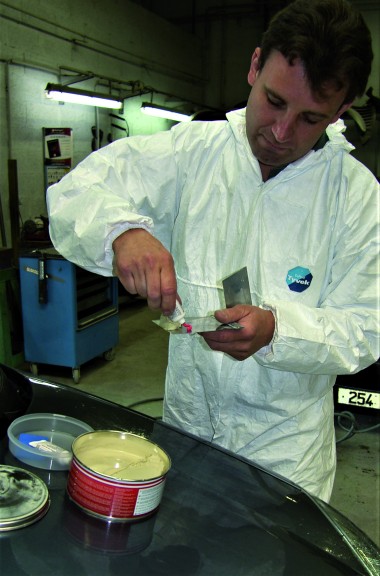
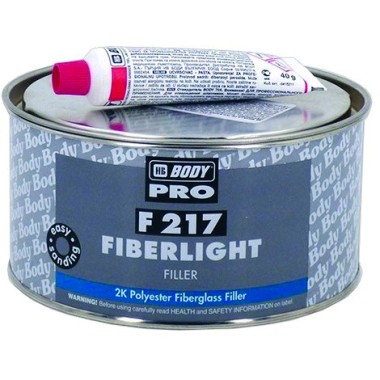
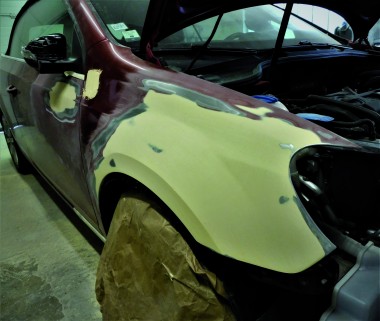
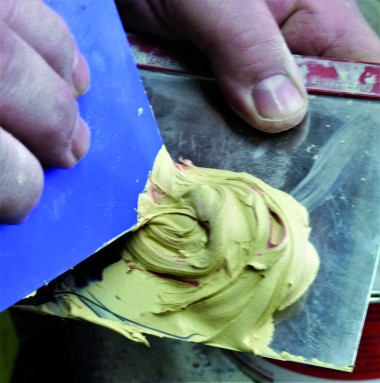
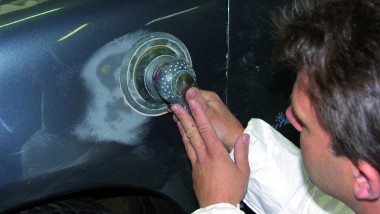
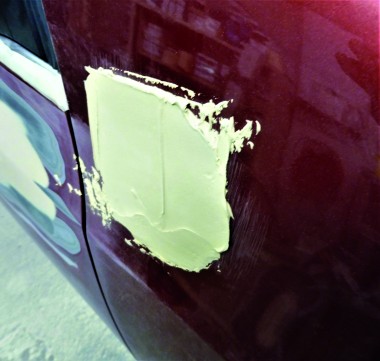
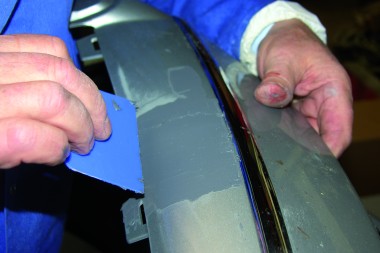
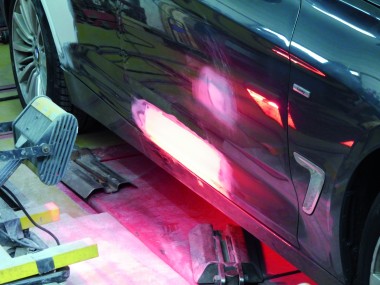

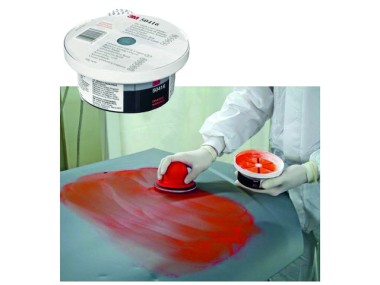
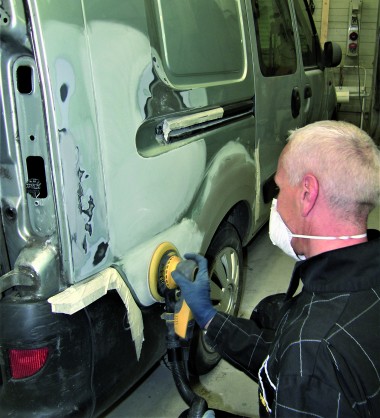
Sur le même sujet
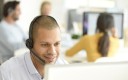
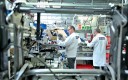
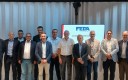
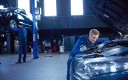